Silicon Photonics Manufacturing Company Accelerates Growth with Intraratio
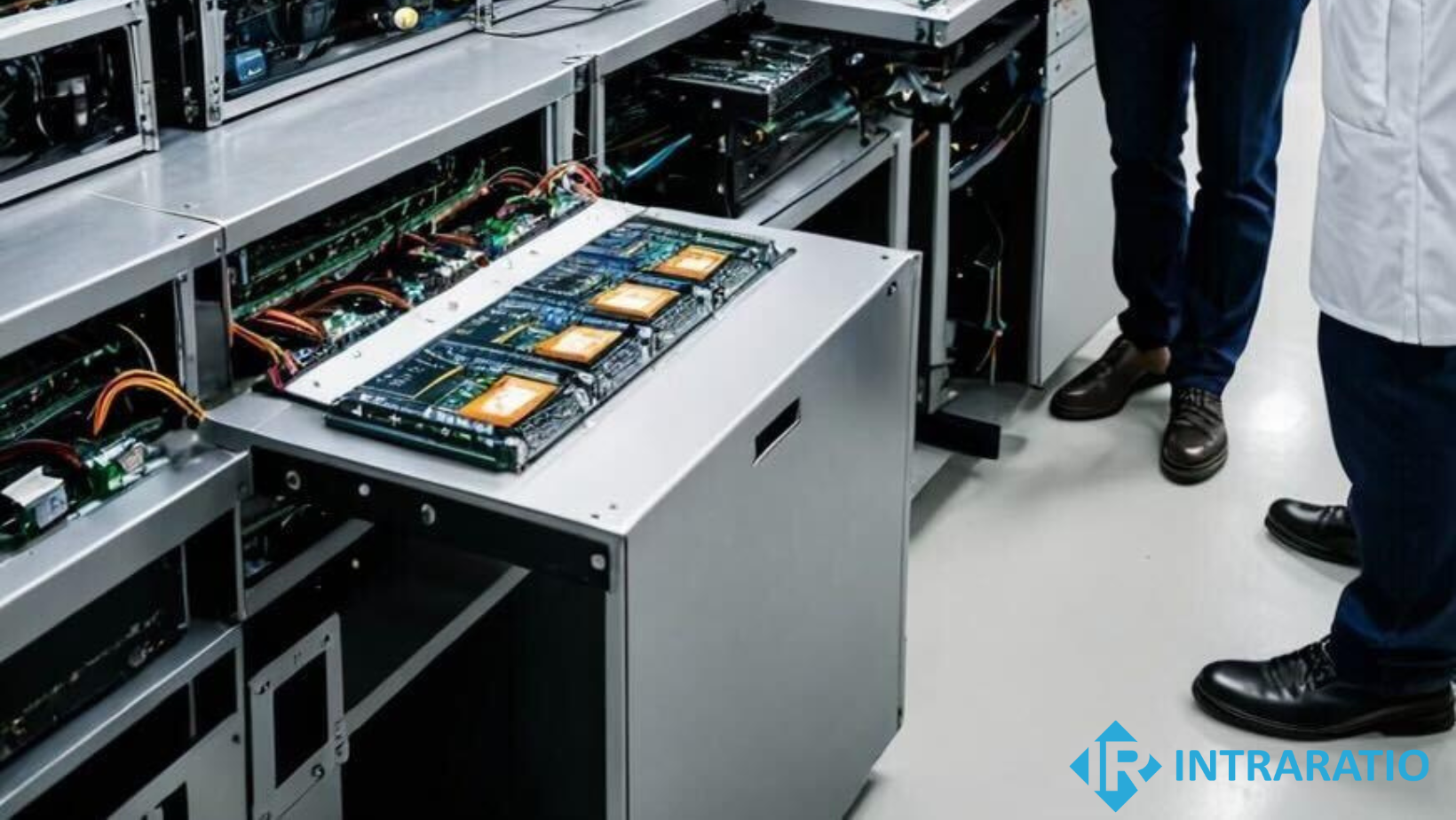
Enabling the next generation of highly integrated systems with silicon photonics (SiPh) based interconnect technologies.
Introduction:
Intraratio is unique in the Global Semiconductor industry with the only known and proven solutions that address the complexities of Silicon Photonics manufacturing.
Silicon Photonics is an evolving industry pushing the boundaries of existing manufacturing capabilities, and is hyper dependent on data integration across the semiconductor ecosystem. This includes data from substrate source, foundries, OSATs, all the way to end products in field deployments where devices are tuned for system interoperability.
Our Silicon Photonics customers are building their own individual and specialized machine systems to perform assembly and test operations that are beyond the scope of traditional vendors. With these capital costs now added to product development cost, they cannot afford the resource and financial impacts of traditional MES providers.
Intraratio is the correct by design solution for today's product technology challenges, with the ability to deploy a true Industry 4.0 solution across any size organization, rapidly, cost effectively and successfully no matter the data challenges. Let's dive into a real-world example to see how Intraratio helped a company achieve truly remarkable results.
Challenge:
A US based Silicon Photonics Manufacturing Company was transitioning from prototype development to volume production. This critical phase, known as the New Product Introduction (NPI) to Volume Production Ramp, requires navigating increasing complexity in manufacturing processes while simultaneously ensuring product quality.
Critical challenges included the following:
- Traceability required across all supply chain points and for in-house factory, of each individual die for each single wafer through their final assembled products.
- New process development included multiple wafer fabrication sources which required data feedback from all downstream operations in order to optimize each foundry process and minimize mask re-spins.
- Assembly processes required automated pick map generation to ensure only KGD were utilized with no bad die placements when performing Chip-on-Wafer (CoW) and Chip-On-Chip-On-Wafer (CoCoW) assembly.
- Advanced quality control was required across all test operations, requiring merging and integration of multiple die test results, ensuring lowest dppm, and guaranteed critical device performance parameters.
- Data infrastructure was required to be self managing to minimize IT support burden, with all necessary connections for data sources, and able to scale seamlessly with production volumes and respective data growth.
- Address workforce constraints due to limited talent pool with specialized industry knowledge: thus required highest levels of data-driven decision automation possible in order to amplify existing workforce capabilities.
Solution:
The company deployed Intraratio's RunCard MES, DataCard YMS and ServiceCard B2B|M2M platform solution for a unified product traceability, analytics, and reporting platform.
Production processes, spanning multiple global assembly and test locations, were mapped into the platform, enabling automated traceability across the entire supply chain.
The following figures provide examples of how a SiPh based device manufacturing process is tracked in the RunCard MES, DataCard YMS and ServiceCard B2B|M2M platform.
Figure 1: Example process complexity managed with Intraratio's solutions
Figure 2: Example data + API connectivity to external suppliers, for real-time global traceabillity of product
Figure 3: Overall IT deployment infrastructure, for low cost high availability and scaleability
Results:
- Faster Time-to-Market: Significantly reduced development cycle time allowed our customer to get their product to market faster than their competition with fully-optimized product performance. This provided a massive competitive edge in the rapidly evolving silicon photonics industry.
- Reduced Product Development and Manufacturing Costs: With automated data collection across all supply chain and manufacturing operations, quality control was automated to identify and address product issues, before subsequent higher cost processes were performed, mitigating undesirable scrap of expensive modules. This enabled rapid product design iteration and ensured manufacturability. This directly translated into fewer returns (RMA), improved customer satisfaction, and rapid market adoption.
- Accelerated Product Optimization: By leveraging hyper-contextualized data and the ability to automate process controls, the company customized product configurations to meet specific customer and market requirements.
- Increased Efficiency and Resource Utilization: Streamlined processes and efficient resource utilization allowed the company to operate more effectively. Comprehensive, secure, accessible, and contextualized data storage enabled both engineering and operations to generate and leverage advanced data analytics. This freed up valuable engineering resources, allowing the company's team to focus on core competencies and strategic initiatives, including focused innovation along with product and process optimization.
- Real-time Supply Chain Visibility: Enabled company to mitigate product quality and delivery risks at all critical production process stages.
Outcome:
Faster time-to-market with higher quality product positioned the company for success in delivering their world-leading new technology to the market.
The company was successfully acquired by a global Tier 1 company for significant transactional value. Operations continued to scale globally, with the acquirer also leveraging Intraratio's solution platform.
Conclusion:
Intraratio's RunCard MES, DataCard YMS and ServiceCard B2B|M2M solutions helped enable the Silicon Photonics Manufacturing Company to overcome the complexities of NPI to Volume Production Ramp. By accelerating product development, improving quality, and optimizing resource utilization. Intraratio's solutions enabled the company's growth and success.
Customer Overview
U.S.-based silicon photonics company, running global operations.